您现在的位置是:Drilling 'Borebots' could finally reach buried Martian life >>正文
Drilling 'Borebots' could finally reach buried Martian life
上海品茶网 - 夜上海最新论坛社区 - 上海千花论坛29524人已围观
简介By subscribing, you agree to our Terms of Use and Policies You may unsubscribe at any time.Engineers...
By subscribing, you agree to our Terms of Use and Policies You may unsubscribe at any time.
Engineers at Planet Enterprises, a Space Technology Incubator in Washington, have revealed a pioneering drilling concept named Borebots, as outlined in a recent NASA report.
These Borebots could usher in a new era of scientific exploration by enabling drilling to unprecedented depths of around 50 meters.
As scientists set their sights on places like Mars' south pole to learn about its ancient water and potential for life, they face the hurdle of extreme depths.
Borebots could change the game by venturing into these depths, helping us uncover even more of Mars' hidden mysteries.
The Borebot fleet
Traditionally, drilling deep boreholes requires complex tethering systems for power and control, resulting in heavy equipment that incurs significant costs.
See Also Related- Captured asteroid secured to solar shield could tackle Earth's rising heat
- Scientists dig rocks in Scotland to learn about Mars samples
- Meals on Mars to be made from plastic waste, says NASA-affiliated 3D food tech expert
- Spot the Dog: The robotic dog busy delivering data on dangerous construction sites for Balfour Beatty
The team at Planet Enterprises, however, devised a new approach—autonomous drilling bots capable of independent operation without the need for tethering.
These compact bots, encased in a 64-millimeter (mm) diameter by 1.1-meter-long cylinder — resembling segments of drilling tubing — embody a range of self-contained components, including a battery, drill bit, motor, and electronic system.
Rovers such as Perseverance (which is currently exploring Mars), or Boston Dynamics Spot robots, could deploy these Borebots. Extending a deployment tube, the rover dispatches a bot to the surface, initiating the drilling process.
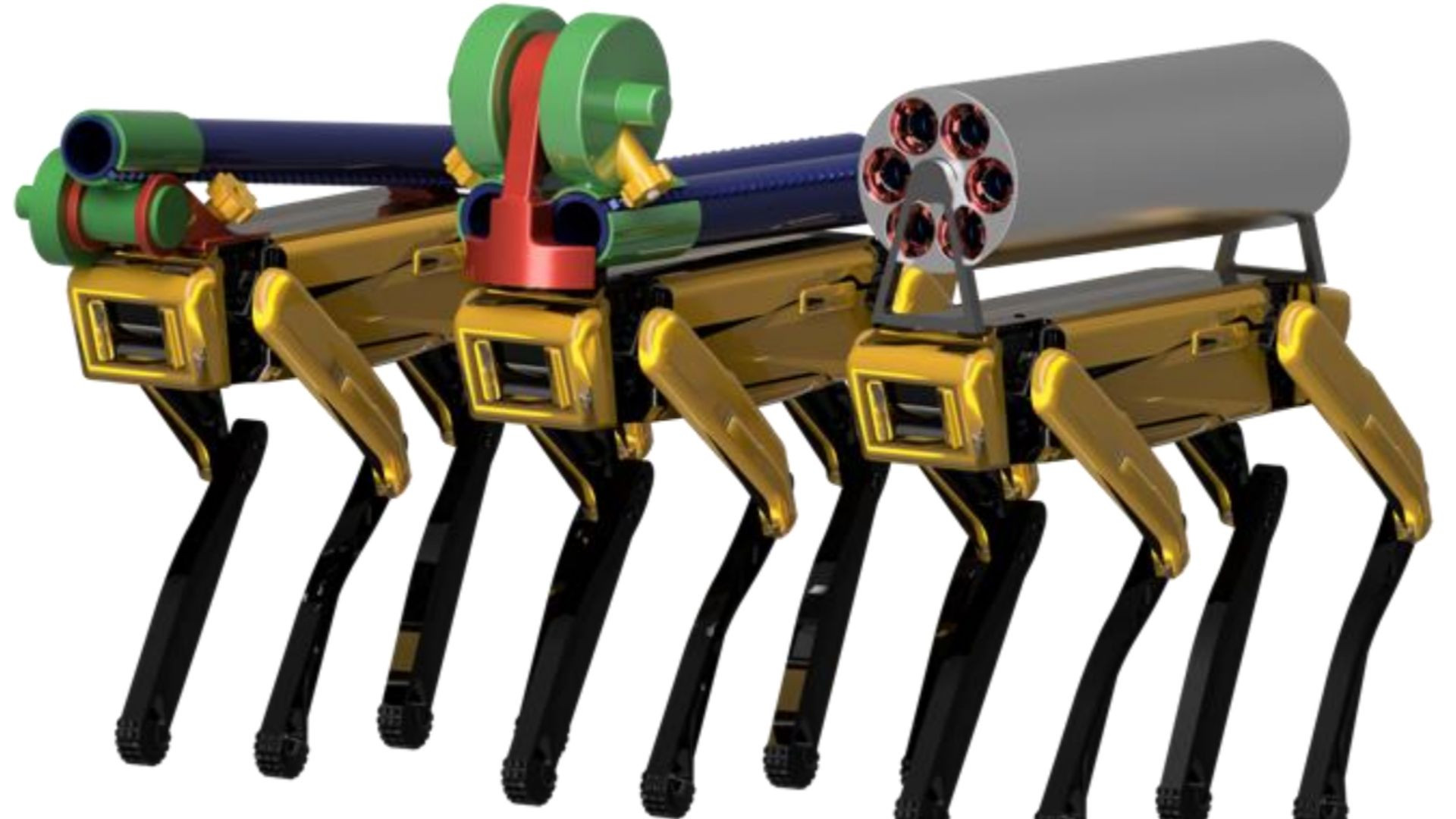
NIAC
Although reliant on battery power, the Borebot's ability to dig through regolith places emphasis on battery life conservation. When energy dwindles, the bot employs traction spikes to ascend back up the hole it created.
Upon re-entering the deployment tube and safely returning to the rover, the Borebot can be recharged and cleaned while another takes its place.
Continuous excavation
With this cyclic system, the Borebot fleet could maintain a continuous excavation rhythm, eliminating the need for bulky support machinery.
The engineering team considered several potential challenges and devised solutions, such as utilizing deceased Borebots to power active ones and introducing articulated joints for branching boreholes.
The comprehensive report includes intricate CAD designs and calculations, spanning power electronics to drill head torque.
While the project's progression remains uncertain, with a lack of apparent further funding, the engineers at Planet Enterprises remain undeterred.
Their visionary ideas, like the TitanAir concept receiving a NIAC Phase I award in 2023, demonstrate their determination to push the boundaries of space technology.
As their pioneering work continues, they're steadily advancing the potential of autonomous drilling and redefining the future of space exploration.
The complete report was published in NIAC and can be accessed here.
Study abstract:
A method is presented for performing deep ice drilling on Mars with an electromechanical drillthat has no physical link to the surface. Whereas cable-suspended electromechanical drills have a tetherto the lander and a system for raising and lowering the drill, this system instead utilizes self-drivingrobots called borebots as the downhole assemblage. This investigation has found several key advantagesto the borebots system, mainly a reduction in single-point-of-failure items like the winch and cable.Instead, several borebots can be used in a sequential mode of operation which evenly distributesmechanical wear and affords time to recharge borebots between trips. This offers the ability to startadditional boreholes at new drill sites when desired, or after a catastrophic loss of downhole equipment.Disadvantages include depth limits due to power storage mass/volume requirements, which can befurther limited by inefficiencies in the borebot drivetrain; and the potential for cumulative wear of theborehole wall which could result in a negative outcome in soft or unconsolidated substrates.
Tags:
转载:欢迎各位朋友分享到网络,但转载请说明文章出处“上海品茶网 - 夜上海最新论坛社区 - 上海千花论坛”。http://www.jz08.com.cn/news/28873.html
相关文章
Australian wind farm to use AI
Drilling 'Borebots' could finally reach buried Martian lifeBy subscribing, you agree to our Terms of Use and Policies You may unsubscribe at any time.Woolnorth...
阅读更多
RoboChem: An autonomous AI robot redefining chemical synthesis
Drilling 'Borebots' could finally reach buried Martian lifeBy subscribing, you agree to our Terms of Use and Policies You may unsubscribe at any time.A team of...
阅读更多
WAVE Charging made 500kW ultrafast wireless EV charging real
Drilling 'Borebots' could finally reach buried Martian lifeBy subscribing, you agree to our Terms of Use and Policies You may unsubscribe at any time.WAVE Char...
阅读更多
热门文章
- Vienna And Singapore Stock Exchanges Support Cryptocurrency
- Exeger's customizable solar cell can offer limitless battery longevity
- Binance Accused of Helping Hackers Launder Stolen Funds
- BTC dips as key support zone at $40k comes under pressure
- Singapore Payments Firm Introduces SGD
- Prinker M+ gives you tattoos and hair coloring on
最新文章
US Judge denies Changpeng Zhao travel to UAE despite $4.5B Binance equity offer
Minesto's Biggest tidal kite Dragon 12 ready to power homes
Bitcoin, Solana, Pullix price prediction as BTC dives below $40k
Bonnaroo 2013 Photo Diary: Wu
Meet Rabbit r1: Your handy AI sidekick turning talk into action
PEPE crashes as SUI pumps 40%; GFOX headed for $5M target