您现在的位置是:Ultrasound 'Pipebots' are tested in a faulty long steel pipe >>正文
Ultrasound 'Pipebots' are tested in a faulty long steel pipe
上海品茶网 - 夜上海最新论坛社区 - 上海千花论坛9575人已围观
简介By subscribing, you agree to our Terms of Use and Policies You may unsubscribe at any time.A team of...
By subscribing, you agree to our Terms of Use and Policies You may unsubscribe at any time.
A team of researchers from the University of Bristol has developed a novel way of inspecting pipes for defects using a network of small robots with ultrasound sensors. The robots can send and receive guided acoustic waves, revealing the presence and location of any flaws in the pipe walls.
The study, published today in NDT and E International, shows how the robots can effectively examine large plate-like structures without requiring communication or synchronization between them. This reduces the data transfer costs and the overall inspection expenses.
Pipebots
The lead author of the study, Dr. Jie Zhang, explained the motivation behind the research: "There are many robotic systems with integrated ultrasound sensors used for automated inspection of pipelines from their inside to allow the pipeline operator to perform required inspections without stopping the flow of product in the pipeline."
See Also Related- These robots travel through underground pipes to help fix blockages
- World’s largest AI robot to reduce aircraft inspection costs
- Alberta Glacier serves as a test bed for NASA's futuristic robotic snake
- Drones are dropping these robot spinning seeds for soil monitoring
However, available systems need help to cope with varying pipe cross-sections or network complexity, inevitably leading to pipeline disruption during inspection. This makes them suitable for specific inspections of high-value assets, such as oil and gas pipelines, but they are only sometimes applicable.
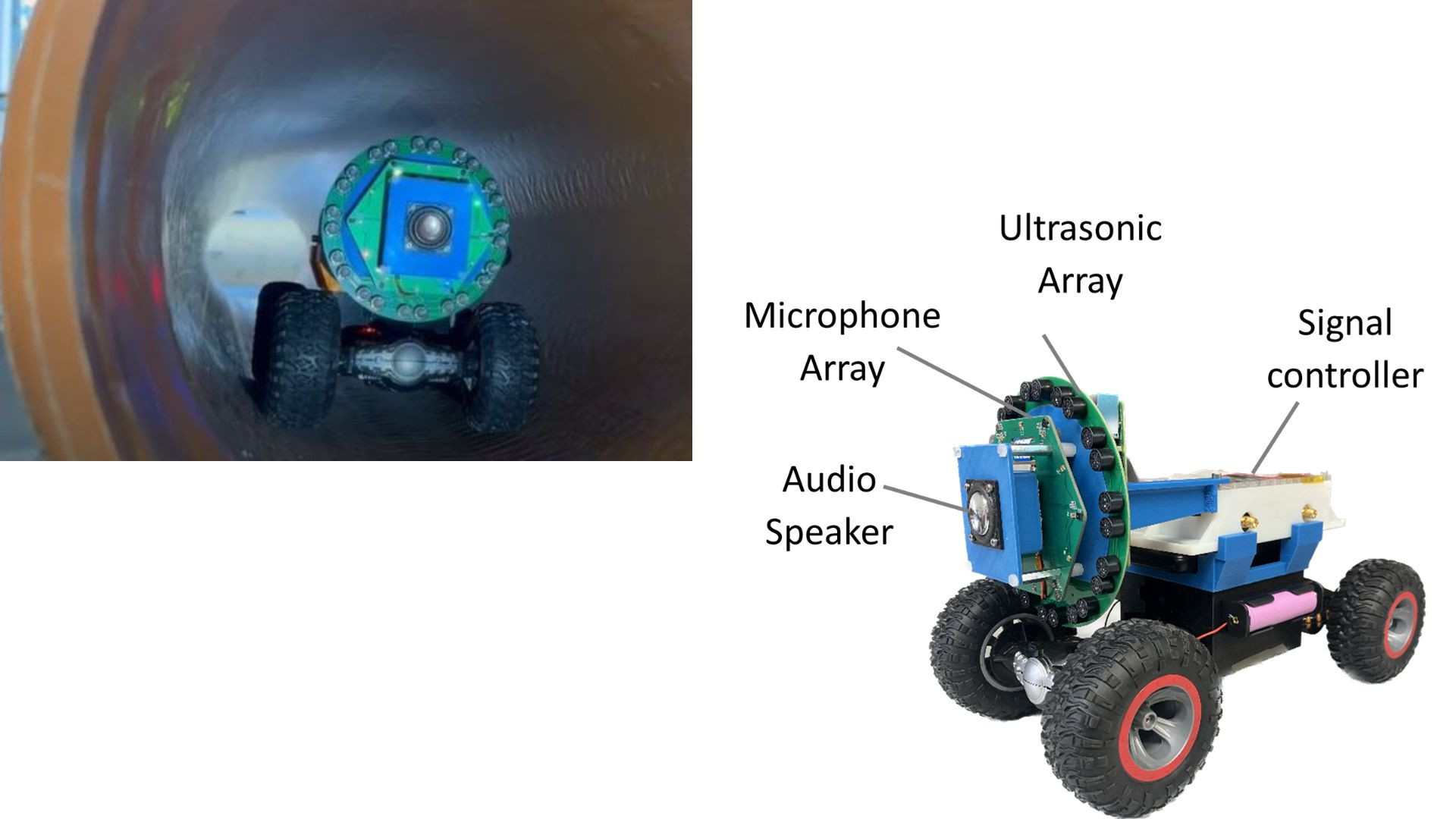
Dr Jie Zhang
"As the cost of mobile robots has reduced over recent years, it is increasingly possible to deploy multiple robots for a large area inspection. We take the existence of small inspection robots as its starting point and explore how they can be used for generic monitoring of a structure. This requires inspection strategies, methodologies, and assessment procedures that can be integrated with the mobile robots for accurate defect detection and localization that is low cost and efficient."
A network of robots has successfully monitored pipes using acoustic wave sensors. 🤖
— University of Bristol (@BristolUni) November 29, 2023
This breakthrough makes them suitable for inspections of oil and gas pipelines, complex underground networks and dangerous sites.
👉 https://t.co/wmynNBcy3U@BristolUniEng@pipebots pic.twitter.com/ALgwWHMhkP
The researchers tested their approach on a long steel pipe with multiple defects, including circular holes of different sizes, a crack-like defect, and pits. They used a designed inspection path to achieve 100% detection coverage for a defined reference defect.
The inspection was divided into two stages: defect detection and defect localization. In the first stage, the robots scanned the pipe using pulse-echo mode, where the same sensor acts as both transmitter and receiver of the acoustic waves. In the second stage, the robots used pitch-catch mode, where one sensor transmits and another sensor receives the acoustic waves. This mode allows the robots to estimate the distance and angle of the defect from the sensors.
Previously, Interesting Engineering covered the broader context surrounding the University of Bristol's Pipebots project, providing a crucial backdrop to the innovative approach developed by the researchers. It emphasized the extensive challenges faced by the U.S., with its 2 million miles of underground pipes and frequent water main breaks causing significant water loss. This underscored the urgency for transformative solutions in pipeline inspection and maintenance.
In light of these challenges, the Pipebots project takes on increased significance. The envisioned 'Pipebots' offers a less invasive and more efficient means of addressing the issues highlighted by Interesting Engineering. The technical insights provided in the coverage, including the robots' autonomous navigation and the use of acoustics for precise mapping, deepen the understanding of the project's technological innovation.
The researchers claim that their methods generally apply to other related scenarios and can be easily adapted to different materials, pipe geometries, noise levels, or guided wave modes.
They also say that their techniques can be used to assess the detection and localization performance for specified inspection parameters, such as the minimum detectable defect size under a given probability of detection and false alarm.
The team, led by Professor Bruce Drinkwater and Professor Anthony Croxford, is now looking for collaboration opportunities with industries to advance their prototypes for actual pipe inspections. This work is funded by the UK's Engineering and Physical Sciences Research Council (EPSRC) as a part of the Pipebots project, which aims to develop a new platform technology for pervasive robotic sensing of buried pipes.
Tags:
转载:欢迎各位朋友分享到网络,但转载请说明文章出处“上海品茶网 - 夜上海最新论坛社区 - 上海千花论坛”。http://www.jz08.com.cn/news/284394.html
相关文章
UK rocket firm approaches first sustainable satellite launch
Ultrasound 'Pipebots' are tested in a faulty long steel pipeBy subscribing, you agree to our Terms of Use and Policies You may unsubscribe at any time.Orbex cou...
阅读更多
Crypto Supporter Nominated For US Comptroller Of Currency
Ultrasound 'Pipebots' are tested in a faulty long steel pipePresident Donald Trump has put forward Brian Brooks’ name to serve as the head bank regulatorI...
阅读更多
Disney Pixar Pals NFTs launched on Veve sells out shortly after launch fetching $3.3M
Ultrasound 'Pipebots' are tested in a faulty long steel pipeDisney Pixar Pals NFTs collectibles launched on March 13 on the digital collectibles marketplace Vev...
阅读更多
热门文章
- Brazil reveals preparation of ipo for digital bank
- US President to sign crypto order focused on regulation and national security
- Blockchain Technology To Be Used To Govern China’s Aerospace City
- Alchemy Pay (ACH) remains in a bearish trend despite recent consolidation
- South Korea To Launch Blockchain Voting System For Elections
- NASA unveils nuclear